Overcrowded warehouses disrupt your workflow, delay tasks, and create unnecessary stress for your team. Piled-up inventory and blocked aisles aren’t just inconveniences — they’re roadblocks to productivity. Addressing these issues is key to running a smooth and profitable operation.
As Chicagoland's custom commercial storage designer, Complete Closet Design has helped countless businesses organize and optimize their spaces. From warehouses to retail backrooms, we’ve seen what works and what doesn’t. In this blog, we’ll share practical tips to help you streamline your storage and improve daily operations.
Tip #1: Analyze Your Current Space Usage
Before making changes to your storage system, gather solid data about how your space is currently used. Many businesses jump into solutions without fully understanding their actual capacity or workflow issues. A detailed analysis reveals where adjustments will have the greatest impact.
Key areas to evaluate:
- Traffic flow: Track the movement of products and people to identify congested paths.
- Storage assessment: Compare your current storage capacity with its full potential.
- Problem spots: Highlight bottlenecks that slow down daily operations.
- Peak periods: Pinpoint times when storage demands are at their highest.
- Vertical analysis: Measure unused overhead space to uncover new storage opportunities.
This data-driven approach provides a solid foundation for your optimization efforts. With clear insights, you can prioritize changes that deliver measurable improvements instead of relying on guesswork.
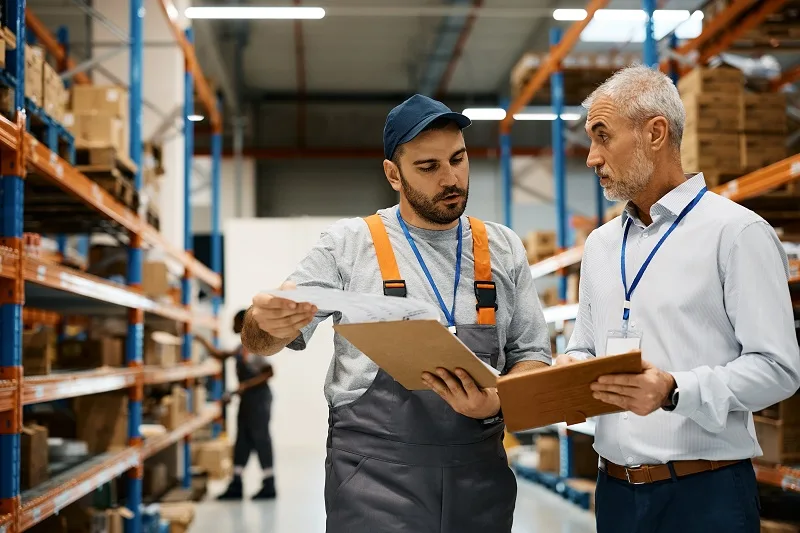
Tip #2: Pick Effective Management Software
The right warehouse management software can transform how your storage system operates. However, many tools are overloaded with features that add complexity and cost without addressing the specific needs of your workflow. Focus on what your team truly needs.
Here’s how to narrow down your options:
- How workers search for products now.
- Which tasks eat up the most time.
- What shipping delays happen most.
- What information managers actually use.
- How orders move through your building.
This shows you exactly what your software needs to do  —  no extra bells and whistles.
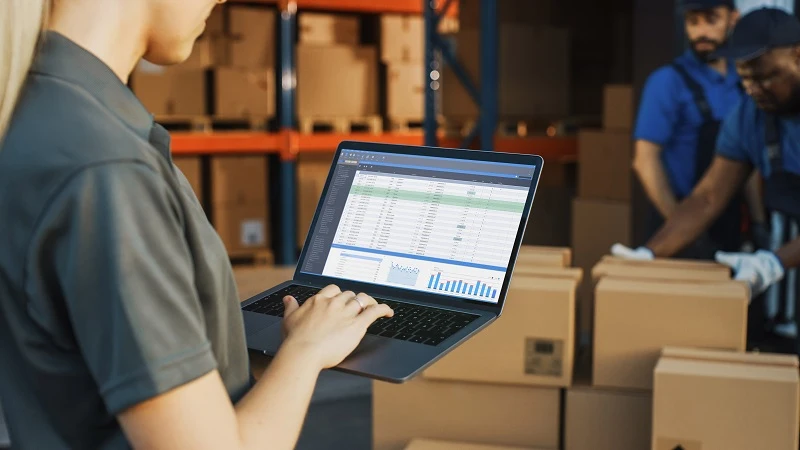
Tip #3: Design Smart Storage Zones
Warehouse needs are constantly shifting. Products phase in and out, sales patterns evolve, and seasonal trends create spikes in demand. Well-organized zones help your space keep up with these changes while ensuring efficiency.
Strategies for smarter zones:
- Speed-based layout: Put quick-selling items in easily accessible front zones near packing areas to minimize travel time and speed up order fulfillment.
- Growth planning: Leave strategic gaps near busy areas to accommodate future expansion. This proactive approach prevents bottlenecks and ensures your storage system can adapt to your business's growth.
- Weight distribution: Place heavy items at waist height to reduce strain during lifting, with lighter items stored higher up for easy access.
- Seasonal rotation: Allocate specific areas for seasonal inventory, with clear processes for transitioning between different product cycles.
- Return management: Dedicate space for handling returned items efficiently, from inspections to restocking or disposal.
Smart zoning is about creating a system that adapts easily to your operations, cutting down on wasted steps and making day-to-day tasks more seamless.
#cta_start
Custom Storage Solutions Are Just a Call Away
Stop working around your space — let it work for you. Contact Complete Closet Design now and discover how custom storage can change everything.
#cta_end
Tip #4: Use Every Inch of Vertical Space
Most warehouse operations ignore their biggest asset — upward space. Walk through any facility and you'll spot the same problem: products and materials crowded on low shelves while valuable overhead space sits empty. Our work with warehouse space optimization has shown that going vertical often doubles storage capacity without requiring extra square footage. But making the most of height takes more than just stacking boxes higher.
- Safety first: Install guardrails, non-slip platforms, and proper lighting to keep elevated storage areas secure for your team.
- The right tools: Use forklifts, rolling ladders, or lift systems that match the size and weight of your inventory for safe and efficient access.
- Label everything: Clear marking systems are essential for quick retrieval and maintaining order across all levels of storage.
- Mix it up: Combine high-rise shelving with other systems, like stackable bins or specialized racks, to maximize versatility.
- Zone smarter: Organize levels by how often items are accessed. Frequently used items stay lower, while rarely accessed stock goes higher.
Turning your focus upward can unlock a surprising amount of extra storage. Many businesses discover they already have the capacity they need — they just weren’t using it effectively.
Tip #5: Let Technology Simplify Your Workflow
Your warehouse doesn’t run on shelves and boxes alone. Digital tools are the backbone of modern warehouse management, but not every software solution is worth the investment. The key is finding tools that match your workflow and make life easier for your team.
Here’s what to prioritize when choosing warehouse management software:
- Track movement: Monitor how products flow through your space to spot inefficiencies and opportunities for improvement.
- Analyze the data: Use analytics to determine the most effective placement for products and to optimize space usage.
- Stock alerts: Set automated notifications to prevent overstocking or running out of key items.
- Performance insights: Measure how different storage zones contribute to overall productivity.
- Integrate systems: Connect your inventory data with shipping and order systems for better planning and execution.
Technology won’t organize your warehouse for you, but the right tools can amplify your efforts and keep your operations running smoothly.
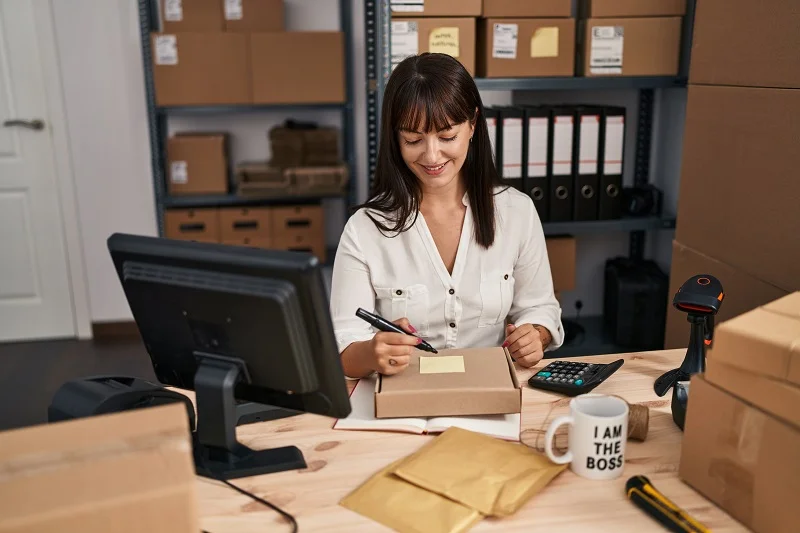
Tip #6: Fix Your Loading Area Layout
Loading docks play a crucial role in the efficiency of your warehouse operations. A disorganized or congested loading dock can slow down the entire process, leading to backups and delays that impact your storage areas. Most loading areas need just a few key improvements to function more effectively — and these changes can often free up a significant amount of usable space.
Start by observing your loading dock in action:
- Document when trucks arrive and depart.
- Time how long it takes to load or unload shipments.
- Note where backups or bottlenecks happen most frequently.
Armed with these insights, you can make targeted changes to optimize the space:
- Clear traffic flow: Set up dedicated lanes for inbound and outbound freight to reduce confusion and delays.
- Staging areas: Create temporary holding zones near dock doors to keep goods organized while awaiting movement.
- Sorting stations: Equip stations with tools to handle various box sizes and types, making the process faster and more efficient.
- Room to move: Ensure forklifts and pallet jacks have enough space to turn and maneuver safely.
- Lighting upgrades: Brighten the area with adequate lighting for visibility during early mornings, late evenings, or poor weather conditions.
Good loading zone organization can prevent storage problems before they start. When products move smoothly from truck to storage (or vice versa), you'll find you have more space and efficiency than you thought possible.
Transform Your Commercial Space Today
Your warehouse should work for you, not against you. When storage is optimized, employees can focus on their tasks without wasting time searching for items or navigating cluttered aisles. Efficiency improves, and customer satisfaction follows.
At Complete Closet Design, we specialize in custom storage solutions that solve real business problems. Whether it’s maximizing vertical space, upgrading your technology, or fixing bottlenecks in your workflow, we’re here to help Chicagoland businesses make every inch count. Contact us today and see how better storage can change the way you work.
Design Your Dream Workbench - Affordable Payment Plans Available!
Don’t let budget concerns hold you back. Design the custom workbench you deserve with our affordable payment plans. Start your project today!